At the start of any project I am a big believer in making prototypes. To make sure this book became the best possible book, I made many prototypes. In fact I made prototypes of the prototypes on the way to making the large fully printed prototype. The first couple of models I made were smaller in page size. I constructed one book simply made of cardboard and copy paper that let me explore the intricate way the pages begin and end in the book. You may never have looked at the very first page in a book before, but it is often a large piece of paper that is glued to the inside cover of the book. This piece is often heavier paper than the rest of the book because it is partially holding the book’s spine together. This page is called the End Paper, and in Vanishing Asia the end papers will be a map of my travels. Getting the sequence of title pages, copyright page, and first page, as well as the sequence at the end was the purpose of this first prototype.
I then made a prototype at the same smaller size but with the full count of pages, each page printed on both sides in black and white ink (to save costs). I then hand-bound the pages with cloth and glue, and a cover with an image on it.
When the smaller page prototype was complete, incorporating the correct order of pages, I handed it over to a professional binder in Oakland, CA as a guide for assembling the full scale prototype.
I had the full book printed in color on an industrial scale color laser printer to the exact final dimensions. I then took this gigantic pile of pages to The Key Printing and Bookbinders in Oakland and they used their cool vintage equipment to bind a single copy of the full book.
You need a hefty machine to cut a stack of 500 pages in one swoop. The folks at Key Bookbinders had the right machine, a scary giant paper cutter that is as dangerous as it looks.
The result of much expertise and hand labor was a single copy of Vanishing Asia. I then shared this copy with some friends who acted as my focus group, and they gave me great feedback. I also shared this single copy with art book publishers to see if they wanted to publish it. (In the end they declined for various reasons.) Along with my own experience in using this single volume, the experience of reading the prototype suggested that breaking it up into 3 thinner volumes would be much better user experience.
Once I had divided the book into three volumes I had a target page count, so I requested our proposed printer to produce a blank prototype of the full size book, using the actual paper type for the book. They use the intended cover material, and full number of pages, at full size to give a very good idea of what the final books will feel and look like. The printers also made a slip case for the full-page count of three volumes. This version of Vanishing Asia was much easier to handle and to read. So that is the format we are used for the final books. (Because of Covid, logistical and political considerations we switched to a different printer after the prototype stage. The printer we chose was Mega Print in Istanbul, Turkey.)
The next step was for Mega Printers to test run about dozen different pages through their printing presses to print sample pages on the exact inks and paper that would be used for the entire book. Those test pages were overnighted to me, and they passed with flying colors. In the meantime a team of printers are combing through the files of the 1,000 plus pages making sure all the t’s are crossed, no pages are missing, and everything hangs together.
Then there is a glorious moment in making a book when you finally sign off on all the pages. You check off the covers, and the pages in between the covers and the end pages. Then you click the button that says “Print it.” Yeah! At that moment, you hope that all the thousand of hours you have spent going over and over the pages, looking at every detail for the tenth time, have paid off and that you have already uncovered the tiny typos, misalignments, dropped margins, forgotten guidelines that needed to be found and removed. Because now everything on those pages will be replicated perfectly, four thousand times.
So in the beginning of July, 2021 I pushed the virtual button and the fancy hi-tech presses at Mega printers in Istanbul, Turkey started turning. At first they printed the cover of the third book in the set. Now there are 4,000 of them. You can see them being replicated in this snap video.
I then arranged the photographs on their positions on each page in the layout software program InDesign, which is what a magazine like Wired would use. I crafted about two dozen different template page designs as a guide, but in fact nearly every page has its own design. I would modify the design on every page to fit the image for that page.
Designing the pages was fun. Keeping track of what images were on what pages and making sure I did not repeat them, or overlook them, was a constant chore. While designing was fun, the task that was the least fun was writing a caption for every image. Captioning was challenging for several reasons. Reason #1 was that I did not have notes of any type, and after 50 years it was hard to remember where exactly a picture was taken. Reason #2 was that very often I had no idea what was really going on in a scene, and so in the process of captioning I wound up going down deep holes of research just to figure out what I had a picture of. It took my half a year to caption all images and I learned almost as much doing that as I did on my travels.
When all the images were placed on the pages and captions written, I had the pages printed out at full scale on a super industrial-scale Epson inkjet printer, with the idea of making a model book. Those pages were then hand-sewn and hand-bound into a massive prototype book. The quality of the digital reproduction was remarkably accurate, pretty much mirroring what I saw on my computer monitor. The master printers of the book in Turkey use a similar digital ink jet printer to create proofs that perfectly match the results that they get from their printing presses. Those proof pages matched my prototype pages, so all was good. Then finally the printers run the actual presses and print a test run of the same test pages on the same paper and inks that will be used later, and the output of those match the proof pages. Photograph, monitor, prototype, proofs, and press tests — all matched and everything lined up, so the printers can print very close to what I saw on my computer monitor. This is the genius of modern printing, where I can expect that the book you will hold in your hand is the book I saw while I was designing it.
Once I saw the results I was delighted by the quality of printing. Today computers control the printing perfectly. It was not always this way. I remember that when my first photobook was printed by artisan printers in Italy 20 years ago, the master craftsmen on the presses would inspect each page and manually dial up or down the inks to get the right level. I stayed in a small room for a week at the printing plant to approve the printing. They printed 24 hours a day, so at night they would wake me to come inspect their color tweeks on the fresh pages. But even that dedicated attention did not produce colors that the computer-controlled presses can produce today — and I no longer need to visit the presses. Vanishing Asia is rife with colors exploding on every page, and this new digital precision allows all the colors to be displayed without the compromises and tradeoffs that have governed color printing in the past.
Running 24 hours a day the printing play quickly piles up 4 million pages, stacked on pallets. As this video taken in the warehouse in Turkey shows, there are a lot of pallets, temporarily wrapped in plastic, as they await binding into books. Stacks of paper as far as one can see. Vanishing Asia is not vanished yet!
The books are too big to fit on the ordinary binding machines, so all 4,000 volumes will be bound by hand. Machines are still involved, but human hands feed the sheets into the smaller machines. The full binding process took about one month.
A huge challenge for this book was designing a shipping carton strong enough to deliver a 26-pound (11.5 kg) book across the oceans and continents without damage. Each book set gets its own shipping carton right from the factory which is used to ship it in the mail. This is no small feat of engineering since the cardboard box must carry this concentrated weight (as much as a sack of concrete) and it can easily ding a book in transit. We went through many iterations, and had the printer test drop boxes in the factory to get a crash-proof design. I even hired a cardboard package designer to come up with one that would protect the fragile corners of the box set.
In the first week of September I got the first advance copy, bound by hand. It was a joy to unbox the first set of books sent from the printer. I cut open the packaging and tried to lift the 3-volume set out of the box. It is surprisingly massive and heavy — be forewarned. Once out and opened, I could see the printed colors are glorious; the images crisp, the paper smooth. I love the sewn binding, which means these huge books lie pretty flat when opened, enabling a full view of the two-page spreads. I spent the next day paging through all 1,080 pages, one by one, to verify the quality is consistent all the way through — and it is! I was happy; the books were fabulous.
This first copy was the approval copy. I gave the printer the OK, so they bound all the printed and folded signatures, and began packing them up onto pallets. There are a lot of books. In the end there will be 3 shipping containers full of books. They are on their way around the world.
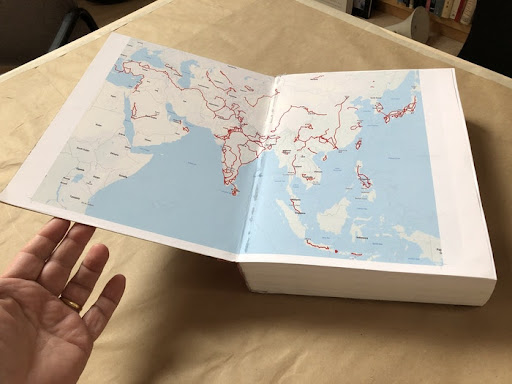

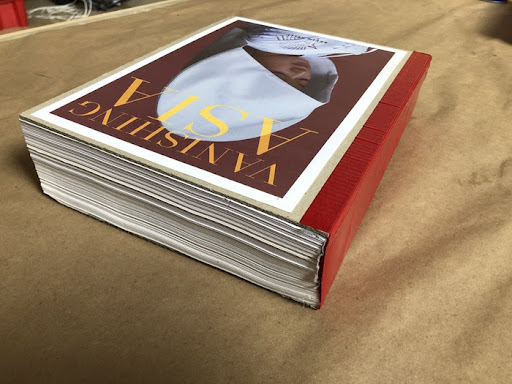
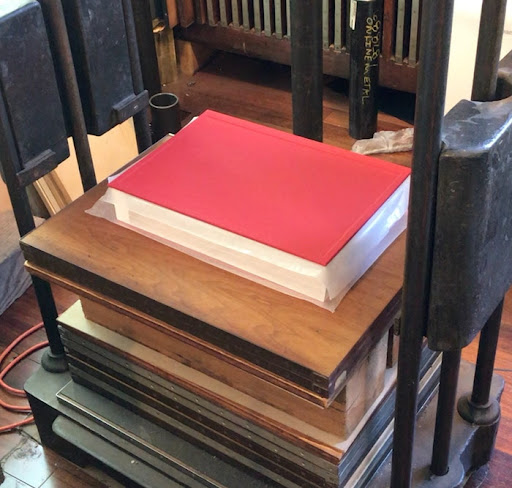
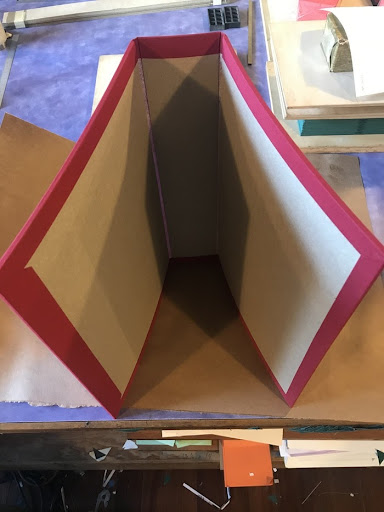
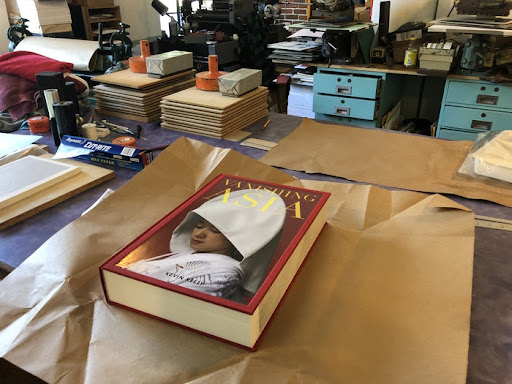
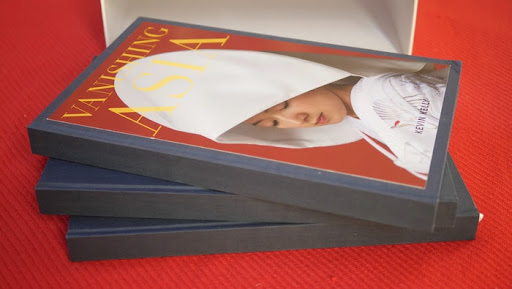